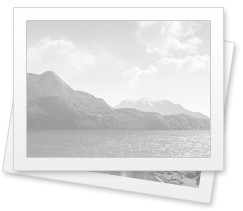
Поливинилхлорид впервые был получен в 1835г Виктором Регно. Основы технологии индустриального производства поливинилхлорида (ПВХ) были разработаны в 1912г Фритцем Клатте. Первые промышленные партии ПВХ были изготовлены вначале 30 годов на заводах США и Германии. Первоначально ПВХ получали, используя широко распространенные и доступные уголь, известь и поваренную соль. Современные технологии предусматривают использование поваренной соли и этилена СН2 = СН2, получаемого в крекинг-процессе переработки нефти. В структуре мирового рынка пластмасс ПВХ занимает второе место после полиэтилена. В Европе доля ПВХ продуктов составляет 28% от общего количества перерабатываемых синтетических материалов. Структура потребления: примерно четверть производимого ПВХ идет на изготовление труб и фитингов, пятая часть на профили из жесткого (непластифицированного) ПВХ - в том числе оконные (http://www.oknarosta.ru/), далее следуют пленки, кабельная продукция, упаковочные материалы и др.
ПВХ обладает наилучшим из всех пластиков соотношением: цена/эксплуатационные качества. Изделия из него обладают долговечностью, стойкостью к атмосферным воздействиям, экологичностью.
Как исходное сырье ПВХ получают в виде мелкого белого порошка. Чистый ПВХ не является конструкционным материалом. Для того, чтобы его переработать в изделие с определенными эксплуатационными качествами, к порошку ПВХ добавляется целая рецептура аддитивов: стабилизаторы, смазки, наполнители, красители, модификаторы.
Стабилизаторы. Переработка ПВХ в готовые изделия производится при повышенных температурах (более 120*С). В этих условиях ПВХ деструктирует с выделением газообразного хлористого водорода. Для предотвращения этого процесса в рецептуру вводят стабилизаторы. В качестве стабилизаторов применяются неорганические и органические соединения свинца, кадмия, бария, олова, кальция и цинка.
Смазки. Смазки необходимы для нормального протекания процесса экструзии ПВХ. Внутренние смазки увеличивают текучесть ПВХ при переходе его в вязкотекучее состояние, а внешние предохраняют смесь от прилипания к горячим металлическим частям оборудования.
Краситель. Универсальным красящим пигментом с высокой разбеливающей способностью является двуокись титана. Именно этот пигмент придает белым профилям яркость и способствует максимальной атмосферостойкости профилей при наружном применении.
Наполнитель. В целях экономии ПВХ в рецептуру добавляется специально обработанный мел. Применение необработанного мела вызывает быстрый абразивный износ металлических частей дорогостоящего экструзионного оборудования.
Модификаторы. Модификаторы служат для придания готовым изделиям из ПВХ ударной прочности.
В небольших и строго рассчитанных количествах в рецептуру ПВХ-смеси вводятся дополнительно антистатики, антипирены, пластификаторы и вспомогательные добавки. Следует подчеркнуть, что для достижения высокого качества профиля и долговечной работы оборудования необходимо строгое соблюдение рецептуры, рекомендованной фирмой-поставщиком этого оборудования, а также соблюдение технологических режимов: температуры давления и скорости экструзии.
В настоящее время производители ПВХ профиля готовят смесь двумя способами:
ПВХ смешивается с компаундом "все в одном", в состав которого входят все необходимые аддитивы для стабилизации и переработки.
Производят смешение всех компонентов самостоятельно. Подбор рецептуры производится методом проб и ошибок и зависит от квалификации химиков-технологов.
В качестве примера современной рецептуры для оконного профиля можно привести следующий состав:
- 100 частей ПВХ
- 5 частей мела
- 5 частей двуокиси титана
- 5.4 частей однопакетного стабилизатора
- 6.5 частей модификатора
Смешение всех компонентов рецептуры проводится в три этапа: смешение в горячем смесителе, смешение в холодном смесителе, выдержка смеси при температуре 15-30*С в течение 24 часов. Подготовленная таким образом смесь подается в экструдер.
Экструзия - это способ изготовления профильных изделий большой длины из пластмасс и резины. Процесс непрерывен и заключается в выдавливании расплава полимера через отверстие определенного сечения. Первый шнековый экструдер для переработки термопластов был создан в Германии в 1935г. Функция экструдера состоит в обеспечении плавления непрерывно подаваемой твердой полимерной смеси, образовании гомогенного вязкого расплава и нагнетания расплава под высоким давлением в профильную головку. Производственная линия включает экструдер, инструмент (фильеру, утройство сухой и влажной калибрации), маркирующий принтер, тянущее утсройство, пилу для резки профиля, устройство для укладки и упаковки готовой продукции.
Подготовленная смесь ПВХ подается в материальный цилиндр экструдера, захватывается шнеком и продвигается по зонам, температура обогрева которых повышается от 150-170C на входе до 190-210C на фильере. В первой зоне происходит перемешивание и предварительный разогрев материала. В следующей зоне пластикации материал переходит в вязкотекучее состояние, уплотняется и поступает в зону дегазации для удаления газообразных включений, захваченного воздуха и влаги. В последней зоне выхода создается давление материала необходимое для прохождения расплава через фильеру.
"Сердцем" всей экструзионной линии по праву считается инструмент: фильера и калибраторы. Именно инструмент в решающей степени определяет качество профиля и требует максимальной тщательности в своем производстве. Фильера состоит из матрицы и дорна, которые формируют щелевой канал протекания расплава. От температурного режима фильеры зависит ровность и глянец профиля. Выходя из фильеры, горячий только что сформированный профиль должен сохранить свою геометрическую форму и быстро охладиться. Для этой цели служат калибраторы: сухой и влажный. В сухом калибраторе горячая заготовка профиля подвергается формовке и охлаждается. Формовка осуществляется путем притягивания профиля к стенкам калибратора за счет легкого вакуума в щелевых шлицах калибратора. Такой вид калибрования называется вакуумным. Для охлаждения поверхности профиля в стенках калибратора расположены каналы для циркуляции холодной воды. Окончательный отвод тепла из всей массы профиля осуществляется во влажном калибраторе, где профиль орошается водой. Далее профиль осушается током воздуха, маркируется на каждом метре и проходит траковое тянущее устройство, скорость которого строго согласуется со скоростью вращения шнеков в экструдере и подачей сырья. Скорость экструзии профилей ПВХ невелика, максимальной считается скорость 8 метров в минуту. Увеличение скорости экструзии может негативно влиять на качество профиля. При существенном увеличении скорости экструзии необходимо пересматривать рецептуру ПВХ- смеси и технологические параметры экструзии.
Заключительным этапом производства ПВХ профиля является автоматическая резка, упаковка и складирование готовой продукции. Ведущими производителями экструзионного оборудования, инструмента и комплектных технологических линий являются фирмы: Cincinnaty, Greiner Technoplast - Австрия; Weber, Вattenfeld, Krauss Maffei - Германия; Amut, Bandera, Buasano - Италия.